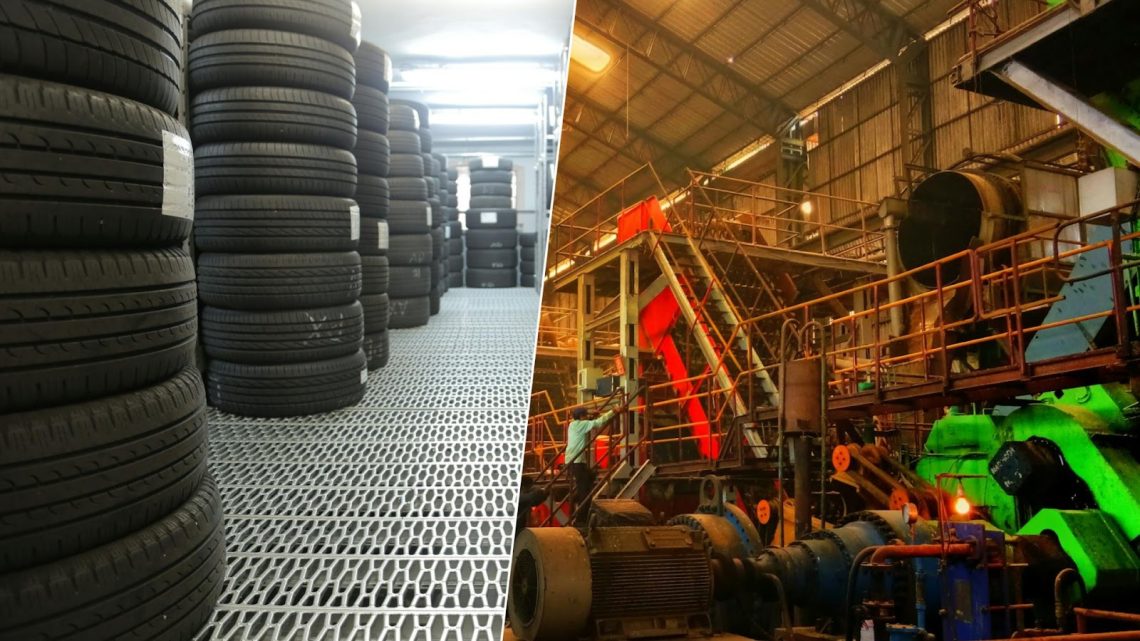
Rubber manufacturing services for industries: How does it work?
*This post may contain affiliate links* or products that have been sent to me for review. You can find out more in my Privacy and Cookie Policy*
This is a collaborative post
Rubber manufacturing is a cornerstone of many industrial processes, providing essential materials that offer durability, flexibility, and resistance to harsh conditions. Industries ranging from automotive to aerospace rely heavily on rubber products for their performance and longevity. The ability to customize rubber components to meet specific industry standards makes rubber manufacturing a versatile and indispensable service. As technology and sustainability practices advance, the role of rubber in industrial manufacturing continues to grow, offering innovative solutions that meet the evolving needs of various sectors.
Why you should choose rubber manufacturing for industrial needs
Rubber manufacturing is a versatile solution for various industrial needs, offering durability and flexibility. Industries rely on rubber for its ability to withstand extreme conditions while maintaining its structural integrity. From automotive to aerospace, rubber components are essential for ensuring safety and efficiency. The production process enables customization to adhere to distinct industry requirements. Choosing rubber manufacturing can significantly enhance the longevity and performance of industrial products. For further information on industrial services, you can explore affarsfokus.com, a helpful resource for industry-related topics.
Durability and flexibility
Rubber is known for its long-lasting durability, making it a preferred choice in industries where materials are subjected to harsh conditions. Its flexibility allows it to be molded into various shapes, fitting perfectly into different applications.
Customization for industry standards
A significant benefit of rubber manufacturing is the capability to tailor products to specific industrial needs. This ensures that each component is tailored to perform optimally in its intended environment.
Different types of rubber used in industrial manufacturing
Various types of rubber are utilized in industrial manufacturing, each possessing unique characteristics. Natural rubber offers excellent tensile strength and is commonly used in products like tires and seals. Synthetic rubbers, such as neoprene and silicone, provide resistance to chemicals and extreme temperatures, making them suitable for specialized applications. The choice of rubber depends on the specific demands of the industry, ensuring that the right material is used for the right purpose. Understanding these differences is crucial in selecting the appropriate rubber for your needs.
Natural rubber
Latex is valued for its high tensile strength and elasticity, derived from natural rubber. Rubber is widely used in industries where strength and flexibility are vital, such as in the production of tires and conveyor belts.
Synthetic rubber
Man-made materials like neoprene and silicone offer properties that natural rubber cannot provide, including synthetic rubbers. They are resistant to chemicals, oils, and extreme temperatures, making them ideal for use in harsh industrial environments.
The key benefits of custom rubber molding for industries
Custom rubber molding offers industries the ability to create parts and components tailored to specific needs. This process allows for precision in manufacturing, ensuring that each piece fits perfectly within its intended application. Custom molding also supports the production of complex shapes that may not be achievable with other materials. Furthermore, it enhances product performance by reducing the need for additional adjustments during assembly. Custom rubber molding provides industries with efficient and cost-effective solutions.
Precision in manufacturing
Custom rubber molding ensures that each part is manufactured with precision, leading to a perfect fit within the larger assembly. This precision minimizes the need for further adjustments, thus conserving time and resources.
Complex shape production
One of the significant advantages of custom rubber molding is the ability to produce complex shapes that are difficult to achieve with other materials. This flexibility allows industries to innovate and create unique components that meet specific requirements.
Selecting the right rubber manufacturing partner
Selecting the right rubber manufacturing partner is crucial for ensuring quality and reliability in your products. Start by assessing the company’s experience and expertise in your industry. It’s important to review their portfolio to understand the range of services they offer. Additionally, consider the company’s capacity to meet your production demands, especially if you require large quantities or specialized products. Communication and transparency are key factors; ensure that your partner is open about their processes and can provide clear timelines and pricing. Finally, check for industry certifications to guarantee that the partner adheres to recognized standards.
Assessing experience and expertise
When selecting a rubber manufacturing partner, it’s important to assess their expertise in your particular field. A partner with relevant expertise will be better equipped to understand your needs and deliver high-quality products.
Reviewing services and capabilities
A thorough review of the manufacturer’s service offerings and capabilities is crucial. Ensure that they can meet your production demands and have the necessary facilities to handle both large and small-scale orders efficiently.
A guide to understanding rubber extrusion processes
Rubber extrusion is a common manufacturing process used to create products with a consistent cross-sectional shape. The process involves forcing unvulcanized rubber through a die, shaping it into the desired form. This method is particularly useful for producing items like seals, gaskets, and hoses. The extrusion process allows for continuous production, making it ideal for high-volume manufacturing. Understanding the basics of rubber extrusion helps in selecting the right process for your product needs and ensuring consistent quality.
How rubber extrusion works
Rubber extrusion involves forcing raw rubber through a mold to form a designated shape. This continuous process is ideal for producing long, uniform products like hoses and gaskets, which require consistent quality throughout.
Advantages of rubber extrusion
A significant advantage of rubber extrusion is its capability to produce large volumes of products swiftly and effectively. This method is economical and facilitates the creation of tailored shapes, making it a flexible option for various industries.
Top rubber manufacturing services in the UK
The UK is home to some of the top rubber manufacturing services, offering a wide range of products tailored to various industrial needs. These companies are known for their expertise, innovation, and commitment to superior craftsmanship. From custom molding to rubber extrusion, they provide solutions that meet the highest industry standards. When choosing a service, it’s important to consider factors such as the company’s reputation, the range of services offered, and their ability to deliver on time. These top manufacturers have established themselves as leaders in the industry, providing reliable and efficient services.
Leading companies in the industry
Several UK-based companies have set themselves apart in the rubber manufacturing industry. These firms are recognized for their advanced technologies, skilled workforce, and ability to handle complex projects with precision.
Comprehensive service offerings
Top rubber manufacturing services in the UK provide a wide array of offerings, from custom molding to high-volume production. This diversity allows them to cater to various industries, ensuring that clients receive tailored solutions that meet their specific needs.
Latest innovations in Rubber Manufacturing Industry
The rubber manufacturing industry is continually evolving, with new innovations driving efficiency and sustainability. Advancements in material science are leading to the development of stronger, more durable rubbers that can withstand extreme conditions. The incorporation of automation and AI in manufacturing is improving accuracy and minimizing waste. These innovations are not only improving product quality but also making the manufacturing process more eco-friendly. Staying updated on these trends is crucial for industries that rely on rubber products to remain competitive.
Advancements in material science
Recent developments in material science are transforming the rubber industry. New formulations are being created to improve the strength, durability, and flexibility of rubber products, making them suitable for even the most demanding industrial applications.
Automation and AI integration
The integration of automation and artificial intelligence in rubber manufacturing is streamlining production processes. These technologies are enhancing precision, reducing errors, and minimizing waste, leading to more efficient and cost-effective manufacturing operations.
The role of rubber in sustainable industrial manufacturing
Rubber plays a significant role in promoting sustainability within industrial manufacturing. The use of eco-friendly rubber materials, such as natural rubber and recycled compounds, helps reduce the environmental impact. Additionally, the durability and long lifespan of rubber products contribute to reducing waste, as they require less frequent replacement. Innovations in rubber recycling processes are also making it easier to repurpose used rubber into new products, further supporting a circular economy. For insights into manufacturing trends and processes, you can also check out Nordic Manufacturing. As industries move towards greener practices, rubber will continue to be a key material in sustainable manufacturing.
Eco-friendly rubber materials
The shift towards using eco-friendly rubber materials, such as natural rubber and recycled compounds, is helping industries reduce their carbon footprint. These materials are not only sustainable but also offer high performance, making them ideal for various industrial applications.
Recycling and reuse initiatives
Rubber recycling initiatives are gaining momentum as industries strive to minimize waste. Advanced recycling processes are enabling the conversion of used rubber into new products, supporting a circular economy and reducing the demand for virgin materials.
Ensuring quality control in rubber manufacturing
Ensuring products adhere to industry benchmarks and function consistently in their intended uses makes quality assurance an essential part of rubber production. Strict testing and inspection protocols are applied throughout the production process, starting from raw material selection to the finished product. These measures help identify and address potential defects before products reach the market. Additionally, manufacturers often adhere to international quality certifications, such as ISO standards, to maintain consistency and trust with their clients. Ensuring high-quality production not only protects end-users but also strengthens the manufacturer’s reputation.
Rigorous testing procedures
Quality control in rubber manufacturing involves rigorous testing procedures to ensure that products meet the required specifications. Tests may include tensile strength, elasticity, and resistance to chemicals, ensuring that the final product is fit for purpose.
Adherence to industry standards
To maintain high standards, rubber manufacturers often adhere to internationally recognized certifications, such as ISO standards. These accreditations assure customers that the products are consistently produced to uphold the highest quality standards.
Finding cost-effective rubber manufacturing solutions
Cost-effectiveness is a key consideration for industries seeking rubber manufacturing solutions. By optimizing production processes and utilizing advanced technologies, manufacturers can offer high-quality products at competitive prices. Bulk production, efficient material usage, and streamlined logistics contribute to reducing costs without compromising on quality. Additionally, partnering with manufacturers who offer customized solutions can help industries avoid unnecessary expenses by ensuring that the products meet specific needs right from the start. Finding a balance between cost and quality is essential for maintaining profitability while achieving industrial goals.
Optimizing production processes
Manufacturers that focus on optimizing their production processes can offer more cost-effective solutions. This may involve using advanced machinery, reducing material waste, and improving workflow efficiency, all of which contribute to lowering production costs.
Customization for cost efficiency
Customizing rubber products to meet specific industry needs can lead to cost savings by eliminating the need for post-production modifications. Tailored solutions ensure that the products are made right the first time, reducing waste and additional expenses.
Industrial rubber manufacturing services in summary
Rubber manufacturing services are crucial for industries that demand high-performance materials tailored to their unique requirements. From the variety of rubber types to the precision of custom molding and extrusion processes, these services provide the flexibility and reliability that industries need to thrive. By choosing the right manufacturing partner and staying informed about the latest innovations, businesses can ensure they are getting the most out of their rubber products. As sustainability and cost-effectiveness become increasingly important, rubber manufacturing will continue to play a vital role in supporting industrial progress.

